Laminat po amatorsku
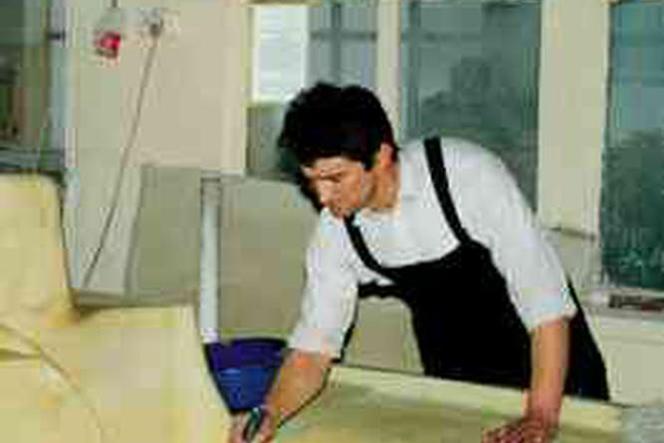
Na wstępie tego cyklu stanowczo odradzałem amatorskiej budowy z laminatów, choćby ze względów tak zwanego BHP. Zdaję sobie jednak sprawe z tego, że rady te i ostrzeżenia wielu puści mimo uszu...
Nie pozostaje więc nic innego, jak - poza przestrogami - spróbować jednak opisać w skrócie najważniejsze metody budowy amatorskiej z laminatów.
Można zbudować bez form jacht skośnodenny z laminatu p-s podobną metodą jak ze sklejki, przez zszywanie i zlaminowanie krawędzi (artykuły w nrach 2, 3, 4/2002 "Żagli"). Przedtem jednak musimy wykonać same segmenty poszycia. I tu znów pojawia się sprawa odpowiedniego projektu! Rzecz się jednak zdecydowanie upraszcza, jeśli dokumentacja zawiera zwymiarowane segmenty poszycia w rozwinięcie. Trzeba je więc najpierw wylaminować na płaskim, idealnie gładkim stole, na którym trasuje się przedtem wyraźnie granice płatów w taki sposób, by przeniosły się na wylaminowane poszycie w sposób trwały, pozwalając na dokładne przycięcie obrysów każdego z płatów burt i dna, np. rysując na niej rysikiem. Rysa bowiem odwzoruje się na poszyciu po wylaminawaniu.
Blat stołu można sporządzić z gładkiej, lakierowanej grubej płyty wiórowej czy tzw. płyty MDF (rys. 1). Blat stołu to jakby powierzchnia formy negatywowej. Musi więc on spełniać kilka podstawowych warunków: być gładki, idealnie płaski i nie zwichrowany. Nie ma też prawa wchłaniać tzw. rozdzielacza, czyli substancji, którą pokrywamy wielokrotnie płytę, rozdzielając żelkot od tej swoistej formy. Zazwyczaj trzeba wylaminować na płycie większą ilość warstw poszycia niż w przypadku jachtów okrągłodennych z laminatu, których poszycie - z powodu krzywoliniowości - wykazuje dużo większą sztywność kształtu niż gięte w jednej tylko płaszczyźnie powierzchnie rozwijalne. Można też się pokusić o zbudowanie tym sposobem kadłuba o konstrukcji przekładkowej. Jeśli wylaminujemy zbyt sztywne płaty poszycia, to będą kłopoty z ich gięciem, podczas łączenia płatów. O sztywności decyduje, przede wszystkim, grubość rdzenia przekładki z pianki Herex czy Airex.
Łączenie płatów odbywa się tak jak w przypadku budowy ze sklejki szytej drutem (rys. 2). Szczególnie staranie należy zlaminować płaty z zewnątrz, zeszlifowując przedtem na odpowiednią głębokość i szerokość krawędzie laminatu. Rzecz w tym, by pasy maty i tkaniny łączące płaty poszycia nie wystawały ponad ich powierzchnię, by można je było jeszcze zaszpachlować żelkotem i wyszlifować.
Pokład to spory problem. Często, w celu uproszczenia, oraz ze względów estetycznych, buduje się go ze sklejki, unikając wytwarzania wielu laminatowych półfabrykatów pokładu o skomplikowanych kształtach.
Kadłuby skośnodenne to jednak pod każdym względem - zwłaszcza hydrodynamicznym i estetycznym - nie to samo co okrągłodenne. Dlatego jachty regatowe buduje się bez formy, opisywaną już na tych łamach metodę tzw. one-off. Można z powodzeniem zastosować ją do wykonania jachtu turystycznego, niekoniecznie, jak w przypadku jednostki regatowej, z żywic epoksydowych, lecz raczej ze zwykłych żywic poliestrowych, znacznie łatwiejszych w przetwarzaniu i bardziej tolerancyjnych na warunki budowy. Otrzymuje się bardziej estetyczny, wytrzymalszy i - co najważniejsze - szybszy, to znaczy o mniejszych oporach hydrodynamicznych kadłub, jednak za cenę sporego nakładu pracy. Jak w każdej metodzie budowy jednostkowej najpierw bowiem trzeba skonstruować tzw. heling (szczegóły w poprzednich artykułach) i postawić na nim szablony wręg. Na szablony te kładzie się następnie sztywne listwy-wzdłużniki co 15 - 20 cm, sprawdzając ich płynność po przymocowaniu do szablonów. Listwy na ogół mocuje się za pomocą gwoździ lub wkrętów we wpustach wyciętych uprzednio w szablonach (rys. 3). Teraz przystępujemy do poszywania takiego ażurowego kopyta płatami pianki PCV - Herexu lub Airexu o grubości przewidzianej przez konstruktora.
Airex należy uznać za właściwszą opcję, gdyż łatwo się gnie na zimno, zaś po podgrzaniu suszarką do włosów lub tzw. opalarką można z jego płatów uformować również powierzchnie nierozwijalne. Nawet duże płyty Airexu daje się dopasować do kształtu kopyta, mocując je do listew za pomocą kawałków drutu, tak aby wszędzie dokładnie przylegały do wzdłużników kopyta i szablonów. Płyty trzeba skleić ze sobą bądź to szpachlówką (najlepiej lekką, na bazie tzw. mikrobalonów), bądź też klejem do termoplastyków. Można się też posłużyć klejem termoplastycznym na gorąco dozowanym ze specjalnego pistoletu.
Po poszyciu całości usuwamy wszelkie kanty i nierówności, zeszlifowując je grubym papierem ściernym lub - co łatwiejsze w przypadku ciągliwego Airexu - strugając nożem lub strugiem.
Teraz można przystąpić do laminowania, zgodnie z tzw. diagramem laminowania, który powinna zawierać dokumentacja konstrukcyjna. Podaje on ilość i rodzaj zbrojenia szklanego w różnych miejscach kadłuba. Po stwardnieniu, czyli w języku fachowym - zżelowaniu laminatu, przygotowuje się kobyłki lub łoże dopasowane do kształtu kadłuba. Teraz odwracamy kadłub wraz z kopytem, odcinamy druty, wyjmujemy kopyto z kadłuba, stawiamy go na uprzednio przygotowanych kobyłkach i laminujemy wewnętrzne warstwy, także oczywiście zgodnie z diagramem laminowania.
Dalej to już tylko same nudy: szlifowanie i szpachlowanie, szlifowanie i szpachlowanie... i tak w kółko, wielokrotnie. A wszystko po to, aby uzyskać błyszczącą i równą powierzchnię po wielokrotnym malowaniu lakierem, koniecznie syntetycznym: poliuretanowym lub epoksydowym.
Podobnie można zbudować pokład jachtu. Niestety i w tym przypadku trzeba się liczyć z tym, że budowa potrwa, bo ilość roboczogodzin na wykonanie samej skorupy trzeba liczyć w setkach, nawet budując tak małą łódkę, jak jacht klasy Micro (ok. 500 roboczogodzin). Trzeba więc mierzyć siły na zamiary, zresztą nie tylko uwzględniając same koszty i pracochłonność, lecz także - co ma niebagatelne znaczenie - swe umiejętności i wiedzę.
Metody jednostkowej budowy z laminatu p-s wymagają ścisłego przestrzegania podstawowych warunków BHP oraz tzw. reżimów technologicznych. Po pierwsze - pomieszczenie, w którym budujemy, powinno być dobrze wentylowane. Najlepiej unikać podejmowania budowy zimą i to
nie tylko z powodu likwidacji w zestawieniu kosztów pozycji "ogrzewanie", ale przede wszystkim ze względu na naturalną wentylację, jaką
w lecie można sobie zapewnić, otwierając wrota hangaru. Zdrowie - najważniejsze!
Opary styrenu nie odkładają się wprawdzie w organizmie, ale przy nadmiernym ich stężeniu można się nimi zatruć. Pracując z żywicami, nie zapominajmy też o nałożeniu rękawic chemoodpornych. Nie ma co ryzykować złapania egzemy lub choćby tylko podrażnienia skóry. Obecnie sprzedawane są
wyłącznie tzw. żywice ekologiczne, o zmniejszonej ewaporyzacji styrenu. Niektóre osoby jednak, zwłaszcza o jasnej karnacji, mają genetycznie uwarunkowane skłonności do uczuleń na styren i inne rozpuszczalniki organiczne.
Od przestrzegania reżimów temperatury i wilgotności w pomieszczeniu, w jakim laminujemy, zależy z kolei jakość laminatu, jego wytrzymałość i sztywność.
Należy powstrzymać się od laminowania, gdy słupek rtęci na termometrze spada poniżej 16-17 stopni lub przekracza 25, gdyż niska temperatura grozi niedotwardzeniem laminatu, za wysoka natomiast - zbyt szybkim jego żelowaniem.
Może to skutkować niesklejeniem poszczególnych warstw laminatu oraz powstawaniem pęcherzy
powietrznych. Duża wilgotność powietrza podczas laminowania także obniża jakość laminatu!